Which Chemical Is Not Manufactured in India? Uncovering India's Chemical Supply Gaps
Walk into a modern Indian factory and it feels like anything’s possible: plastics, dyes, fertilizers, even pharmaceuticals flow from local production lines. India’s chemical industry is a beast—one of the world’s top exporters and a vital cog for countless other sectors. But not everything is homegrown. Despite all the progress, a surprising number of vital chemicals aren’t made within India’s borders. Some are exotic, a few are essential, and others leave the nation relying on foreign suppliers. Why can’t India make everything—especially in a country that seems to manufacture nearly anything? Let’s dig into the heart of this paradox, where hard economics meets raw chemistry and global politics. There’s more hiding in India’s chemical story than most people realize.
Why Aren’t All Chemicals Manufactured in India?
It might sound odd at first. India is basically the world’s pharmacy and the production hub for dyes, pesticides, and plastics. So why isn’t everything made here? A mix of reasons: technology gaps, raw material shortages, high costs, licensing hurdles, international agreements, and surprisingly, environmental rules. Many chemicals—especially advanced specialty chemicals and some raw pharmaceutical ingredients (APIs)—require cutting-edge equipment and know-how. For example, fluorochemicals like perfluorooctanoic acid (PFOA), used in high-performance coatings, need tech India is still working on. Then there’s melamine—used for making fire-resistant plastics. Until recently, it was entirely imported because of raw material constraints.
The story gets even stickier with rare earth metals and advanced electronics chemicals. Take gallium, used for semiconductors and LEDs. India has no large-scale commercial gallium extraction or refining capacity, so almost everything gets imported from China or Europe. Some chemicals are simply too expensive or hazardous for Indian firms to bother with. Toxic feedstocks like phosgene or allyl chloride involve serious risks and require multi-million-dollar investments in safety systems just to make on a global scale. These capital barriers shut out all but a few leading multinationals.
Policy sometimes blocks production. Certain chemicals—like those on global anti-proliferation lists (think missile fuels or agents on the Chemical Weapons Convention)—are off-limits for commercial production beyond tiny research quantities. Even simple compounds such as potassium cyanide or some hydrazine derivatives are highly regulated, so you won’t find anyone casually whipping them up. Then comes the environmental side. Let’s talk CFCs (chlorofluorocarbons), once common in refrigerators and aerosols. India banned producing most CFCs under its Montreal Protocol commitments to fight ozone depletion, so these are only available as imports for research or certain medical uses under heavy restriction.
Add to that the patent minefield. Tons of modern specialty chemicals and pharmaceutical intermediates are protected by global intellectual property rules, blocking Indian firms from setting up domestic production. The lack of continuous, reliable feedstock or relevant technology means firms either import finished chemicals or their key intermediates. Sometimes it’s plain economics—a tiny home demand, huge investment needed, and limited profits. In other words, if it’s cheaper to buy it than make it, supply chains will just import.
Here’s the human side: chemical manufacturing at scale is loud, messy, and risky. It needs skilled chemists, seasoned process engineers, and a workforce trained for tough environments. Sourcing the right technical expertise sometimes means working with partners abroad. The Indian government has pushed for more self-sufficiency through schemes like "Make in India." Still, gaps persist, especially in ultra-high-purity chemicals and advanced APIs, keeping India reliant on imports for some big-ticket molecules.
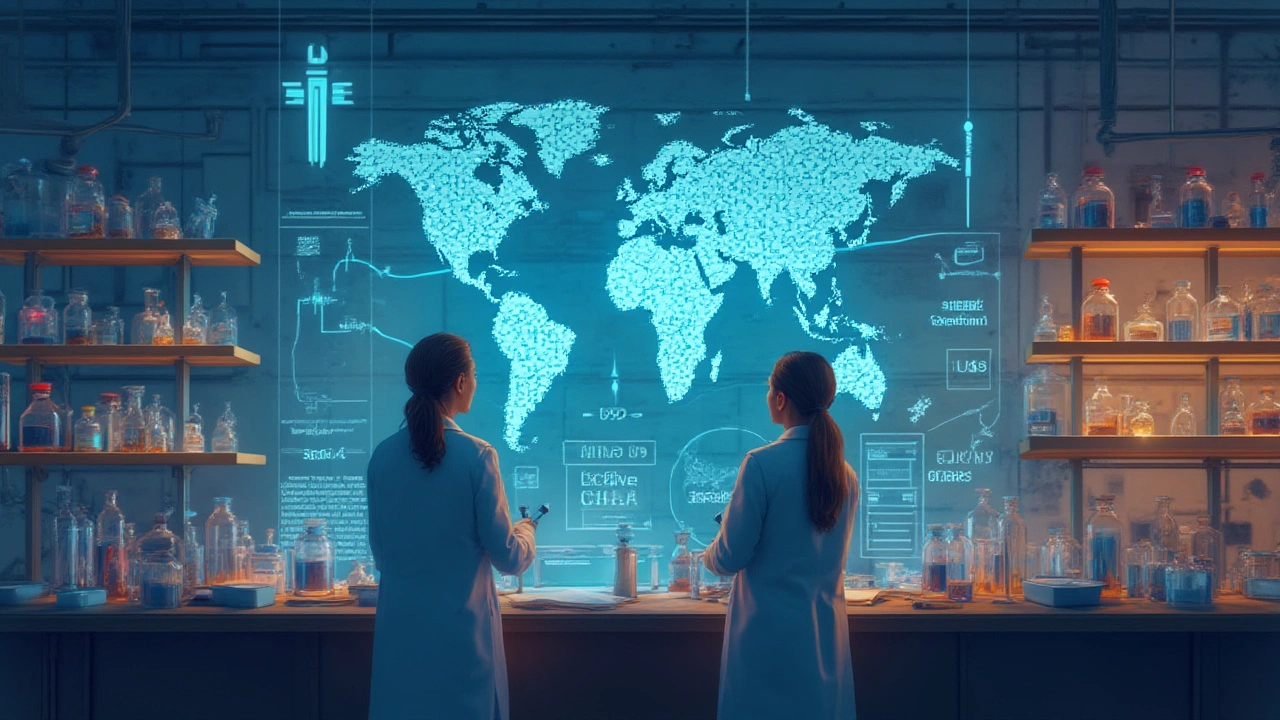
The Known List: Chemicals India Doesn’t Manufacture
So, which chemicals aren’t made locally? Unlike off-the-cuff lists, let’s stick to specifics, with facts from trade and industry reports, and what’s flagged by India’s Chemical and Fertilizers Ministry:
- Potassium Nitrate (KNO3): Once produced locally, India now relies almost entirely on imports—mainly from China, Chile, and Israel. This salt is essential for fertilizers, fireworks, explosives, and food preservation.
- Bismuth Compounds: Used in advanced pharmaceuticals and fire detection, these are not manufactured in India at scale. The country imports the majority of bismuth oxide and subnitrate, primarily from China and South Korea.
- Gallium and Gallium Compounds: No domestic manufacturer runs anything close to commercial-scale gallium production. India brings in gallium, gallium arsenide, and their derivatives for use in LEDs, solar panels, and advanced electronics from Germany, China, and the US.
- Perfluorochemicals: Some ultra-pure fluorochemicals (for instance, perfluorooctanesulfonic acid or PFOS) needed in electronics, aerospace lubricants, and specialty coatings have zero Indian supply. These are imported, often from Japan and Western Europe.
- Melamine (until 2022): India was wholly dependent on imports (especially from China) for this key plastic-making chemical until Gujarat State Fertilizers & Chemicals set up a plant. Still, demand outpaces supply, so most melamine is imported.
- Phosgene-based Intermediates: While India produces phosgene in limited quantities, the downstream fine intermediates like diphenyl carbonate (used for polycarbonates) are mainly imported owing to safety and tech barriers.
- Ultra-Pure Hydrofluoric Acid: Needed for making semiconductors, it’s not locally available at electronic-grade purity; almost all stocks come from Japan, Taiwan, or South Korea.
- Rare Earth Salts and Lanthanide Compounds: Everything from dysprosium oxide to yttrium nitrate—critical in advanced magnets, lasers, and battery tech—is heavily imported, mostly from China.
- Silicon Wafers and Monocrystalline Silicon: Not exactly a chemical, but these are totally imported for India’s electronics and solar cell factories, due to the lack of commercial-scale manufacturing.
- Peptide and Oligonucleotide APIs: Key ingredients for modern biotech drugs, India is still building up the know-how; right now, major pharma companies import most of these specialized molecules from the US and Europe.
- Custom Pesticide Intermediates: New-generation agrochemical intermediates (especially for non-generic, patented molecules) often have no Indian manufacturing base and must be sourced from China or Europe.
Now, this doesn’t mean every last drop is imported, there may be some lab-scale production or niche vendors, but absolutely no large-scale domestic makers. To get a sense of the dependency, trade numbers don’t lie. According to the Ministry of Commerce’s Exim data for FY2023-24, India spent $31.2 billion on importing chemicals, with a notable chunk being specialty or advanced intermediates never made locally.
Chemical | Main Use | Top Source Countries | 100% Imported (Y/N) |
---|---|---|---|
Gallium & Compounds | LEDs, Semiconductors | China, Germany, USA | Yes |
Ultra-Pure Hydrofluoric Acid | Chips, Solar Cells | Japan, S. Korea, Taiwan | Yes |
Potassium Nitrate | Fertilizers, Food Processing | China, Israel, Chile | Yes |
Bismuth Salts | Pharma, Electronics | China, S. Korea | Yes |
Custom Peptide APIs | Pharmaceuticals | USA, Europe | Yes |
This matters more than most people guess. If a supply crunch or political upset blocks a key chemical, entire industries and thousands of jobs are at risk. For example, India’s semiconductor ambitions hit a roadblock not just from tech, but from the inability to make ultra-pure etching chemicals locally. Same goes for pharmaceutical innovation, which is partly hamstrung by the need to import rare APIs and advanced intermediates.
That’s not all. Some highly specialized catalysts, photoresists, fluoropolymers, and non-generic agrochemicals are simply unavailable without imports. Small-quantity specialty chemicals for R&D come almost entirely from abroad, courtesy of companies like Sigma-Aldrich or Merck. So, while the shelves of chemical markets in Mumbai and Ahmedabad show dizzying variety, a put-you-on-the-spot quiz on truly locally made chemicals quickly comes up short in these areas.
Want a tip? For manufacturers thinking of entering these spaces, check India’s import trade stats—chemicals with a 100% import ratio and rising demand mean less competition and a real chance for local companies to cash in if they can crack the tech and scale.
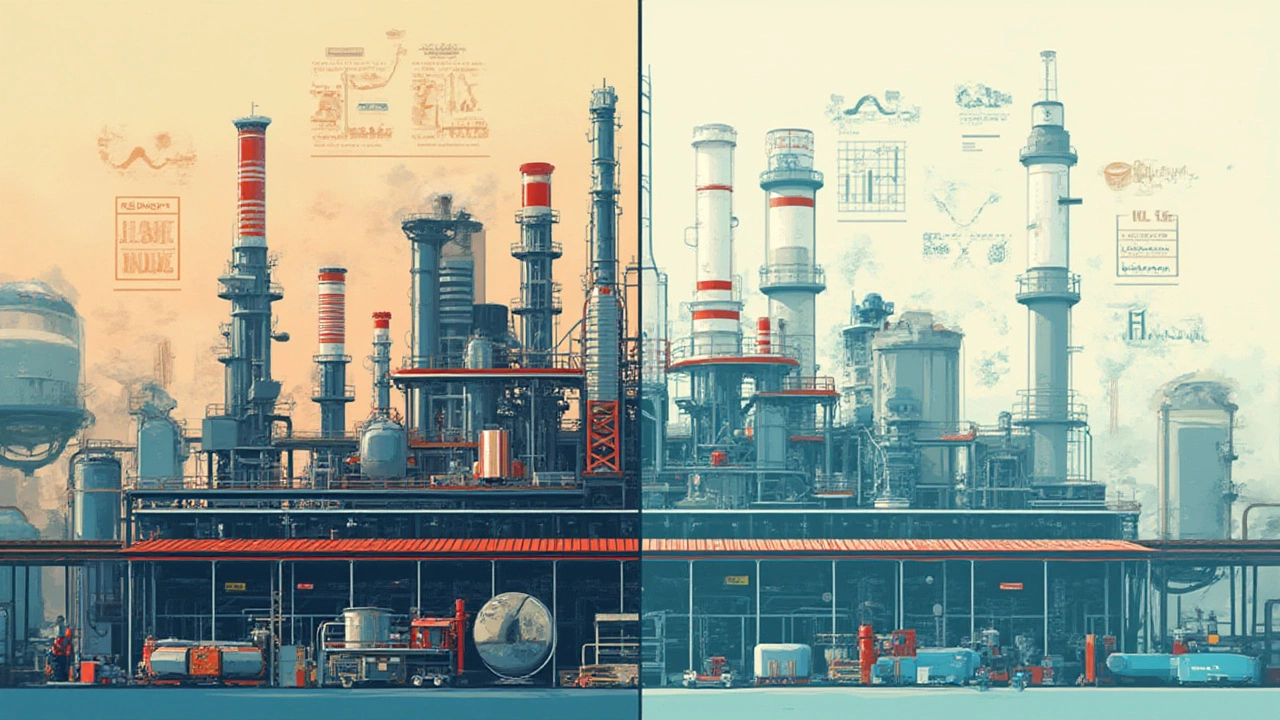
Can India Bridge These Gaps—And Should It?
So here’s the million-rupee question: will India ever make every chemical it needs? There’s a burst of activity in government and private industry. The push to cut import reliance is real. Initiatives under "Atmanirbhar Bharat" (Self-reliant India) and PLI (Production Linked Incentive) schemes are swinging into action. For instance, new projects in Dahej (Gujarat) and Paradeep (Odisha) are gearing up to make more APIs, specialty polymers, and intermediates. Government-backed research, in places like the National Chemical Laboratory (NCL) and the Indian Institute of Chemical Technology (IICT), is aiming to close some tech gaps, especially in clean-room fluorochemicals and photopolymers.
It’s not just about big business—smaller Indian firms are trying to move up the value chain. They scout global patents that are expiring, team up with multinational partners, and hunt for Foreign Direct Investment (FDI) in advanced chemical plants. These moves help boost the country’s tech muscle and know-how. Each successful shift away from imports not only saves money but also insulates industries from export bans, shipping messes, or unpredictable geopolitics.
Still, bridging chemical gaps comes with big challenges. Manufacturing something like ultra-high-purity gallium or PFOS isn’t cheap or quick. It demands hand-in-glove partnerships between government, academia, and industry, plus serious capital and long-term market vision. Then there’s the human element: a pipeline of skilled chemists, chemical engineers, safety managers, and environmental scientists—the real power behind any world-class chemical industry. India’s universities are beefing up curriculum and research to feed this pipeline, but results take time.
The risk? If India rushes in, ignoring pollution or safety norms, disasters like Bhopal could repeat. So, the tightrope walk continues—expand local chemical capacity without trading off health or environment. On the flip side, every time India makes a chemical it previously imported, it not only secures supply but often creates hundreds or thousands of jobs, boosts exports, and forges new technology ecosystems.
What about alternatives? Sometimes, Indian researchers find ways to sidestep unavailable chemicals altogether by innovating with local or green alternatives. Bio-based routes, catalysis upgrades, or even shifting to entirely different process pathways are on the table. An example: instead of traditional, imported platinum group catalysts, Indian R&D is working on copper- or nickel-based alternatives for select syntheses. Such home-grown tweaks won’t solve the rare earth puzzle, but they push the boundaries in nutrition, pharma, and even electronics.
A practical tip for entrepreneurs, students, or investors: keep your eyes on government tender documents, research grants, and demand projections from India’s Department of Chemicals and Petrochemicals or the Pharma Export Council. These sources flag which chemicals are next on the target list for homegrown production—and where the money is headed.
To sum up, India’s chemistry map is a mix of brag-worthy local giants and strategic blind spots. For the chemicals listed above, the country still depends on imports. Every new factory, tech tie-up, and R&D breakthrough helps shrink that list. And for anyone wanting a front-row seat to the next big thing in Indian industry, it pays to watch which chemicals are still "import only." There’s opportunity in those supply gaps—if you know where to look.