Semiconductors Made in India: What's Actually Happening?
If you live in India, own any gadgets, or keep up with tech news, you’ve probably heard big promises about homegrown semiconductors. It sounds impressive, right? India is pushing hard to get its own chips made locally—not just for phones, but for cars, appliances, and national security.
But here's the thing most headlines skip: as of now, India still does not mass-produce advanced semiconductors like Taiwan or South Korea. That doesn't mean nothing is happening—there’s plenty of action behind the scenes.
The Dholera Mega Fab, Tata Group’s plans with Taiwan’s PSMC, and a few government pilot plants are all making noise. Still, most actual chips labeled as “Made in India” turn out to be designed locally but fabricated somewhere else. Packaging and testing? That’s happening here, sure. But the core high-end manufacturing—the real magic—still tends to be imported.
If you’re in electronics manufacturing, sourcing parts, or just curious where your phone’s brain comes from, what’s going on with semiconductors in India actually matters. It means jobs, less reliance on imports, and major ripple effects through the tech scene.
- India’s Chip Dream: Where It All Began
- Major Semiconductor Projects: Reality Check
- The Real Meaning of 'Made in India' Chips
- Challenges Holding India Back
- What to Watch If You Care About Semiconductors
India’s Chip Dream: Where It All Began
Back in the 1980s, India saw the future of electronics manufacturing and wanted a piece of the pie. The government kicked things off with a facility called Semiconductor Complex Limited (SCL) in Mohali, Punjab. This place was set up to make India self-reliant for things like chips used in telecom and defense gear. After a fire in 1989, SCL got rebuilt, but never grew big enough to meet industry needs—most tech companies still had to import advanced chips.
It wasn’t for a lack of trying. Since the 2000s, India has rolled out policy after policy—the Special Incentive Package Scheme, Make in India, and the more recent Production Linked Incentives (PLI) for semiconductor players. The idea? Get big brands and startups to build chip factories (fabs) on Indian soil.
Here’s the kicker: India quickly became a global talent hub for chip design, with homegrown engineers working in offices for giants like Intel, Qualcomm, and Texas Instruments. But those designs would then queue up for production in Taiwan or South Korea. Actual chip production in India never hit the big leagues.
Just to give you a sense of where things stood, check out how India compared to global chip powerhouses in 2023:
Country | Annual Semiconductor Output (%) |
---|---|
Taiwan | ~60% |
South Korea | ~20% |
USA | ~10% |
India | < 0.1% |
The dream was always big—a real India semiconductor ecosystem that could power phones, computers, and even satellites. But for decades, it mostly stayed a dream.
Major Semiconductor Projects: Reality Check
So, where’s the real action when it comes to India and semiconductor manufacturing? You’ve probably heard about multi-billion dollar projects getting green-lighted, but the reality is a mix of hope, new ground, and a bit of stubborn old India.
Let’s start with the Tata-PSMC project. Early in 2024, Tata Group made headlines by teaming up with Taiwan’s Powerchip Semiconductor Manufacturing Corporation (PSMC) to build a fab in Dholera, Gujarat. This one got the government’s nod and billions in incentives. The plan? Make 28nm and older nodes at scale. But—and it’s a big but—they haven’t produced even test wafers yet. Best case, the first chips might roll out around 2026 if everything goes to plan.
Then you’ve got the Micron plant also in Gujarat. This one’s a bit different—it focuses on assembling and testing memory chips, not manufacturing the actual wafers. The plant started limited operations in 2023, handling packaging for memory products. Big step for job creation, but the real chip-making—the silicon part—still happens offshore.
Another project you might have read about is ISRO’s fab in Chandigarh. It’s been making small batches for defense and research, but calling these mass-produced or commercial chips would be a stretch. They’re more about niche applications, and the volumes are tiny compared to what global giants pump out.
Here’s a quick look at what’s actually going on with the big players:
Project | Location | Status (May 2025) | Type |
---|---|---|---|
Tata-PSMC | Dholera, Gujarat | Fab construction started, no chips yet | Integrated circuits, 28nm+ |
Micron | Sanand, Gujarat | Packaging & testing running | Memory modules (no wafer fabrication) |
ISRO SCL | Chandigarh | Pilot/defense batches | Older tech, niche chips |
If you’re hoping to buy a Made in India phone or laptop knowing the chips are truly Indian, hold that thought. The country is on the move, but real large-scale chip production isn’t here yet.
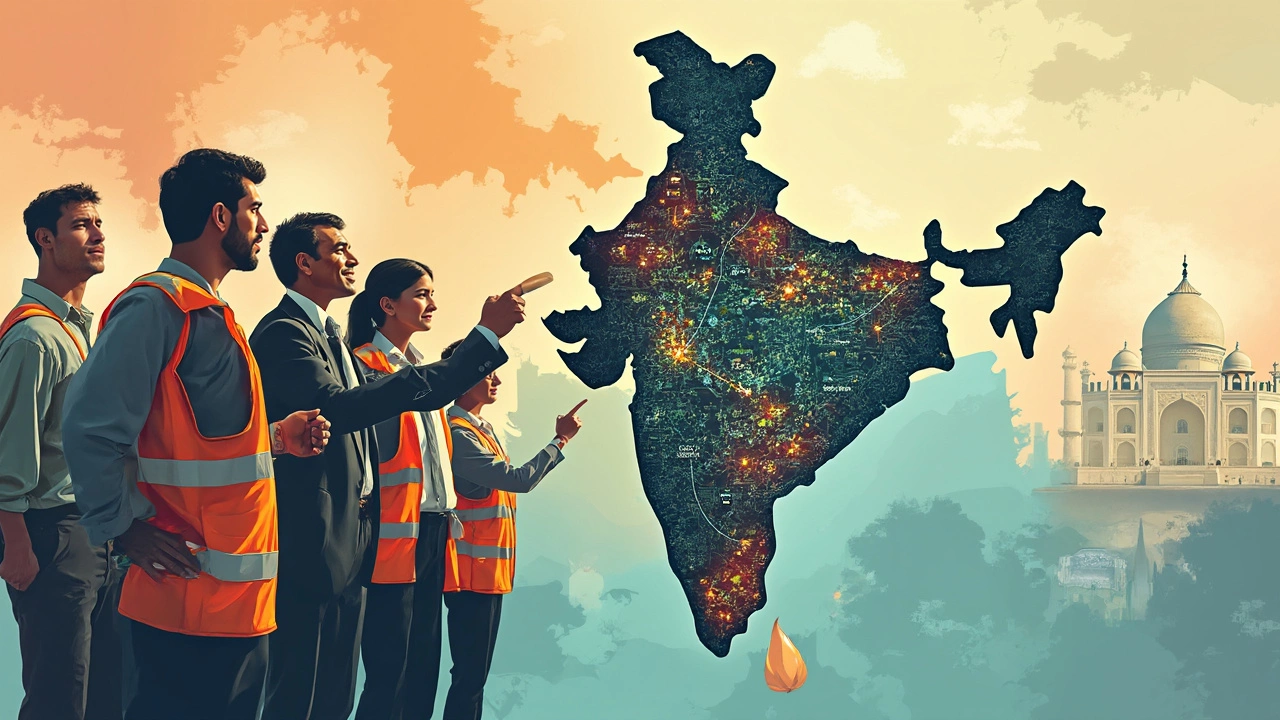
The Real Meaning of 'Made in India' Chips
When you see a label that says a chip is "Made in India," it doesn't always mean the whole process happened here. It’s more complicated than that. Churning out semiconductors involves a lot of stages, from designing and making the chip itself to testing and packaging. Right now, most of the action happening in India focuses on chip design and backend work, not actual silicon wafer fabrication.
Multinationals like Intel and Texas Instruments have huge design teams in Bengaluru and Noida. They’re designing some impressive stuff, for sure. But when it’s time to actually manufacture these chips, almost all that work gets done in foundries in Taiwan, South Korea, or the US. The silicon is then shipped back to India where local companies handle the packaging, testing, and sometimes assembly into final products.
If you break down what’s really happening under that Made in India tag, here’s how it typically looks:
- Chip Design: Many chips for phones, appliances, and even electric cars are designed by Indian teams.
- Fabrication: Actual manufacturing of the chip (wafer fabrication) still happens outside India.
- Packaging & Testing: Companies like SPEL Semiconductors in Chennai and SCL in Mohali do the assembly, packaging, and test phases.
What about large-scale local fabrication? As of May 2025, India’s first full-scale semiconductor factory—the Tata Electronics and PSMC (Taiwan) partnership in Dholera—has just broken ground but won’t produce chips until at least 2026. The ISRO-supported SCL in Mohali mainly focuses on specialized chips for space and defense, not consumer gadgets.
It helps to look at what’s actually being produced today:
Step | India Status (2025) |
---|---|
Chip Design | Strong, lots of talent, global impact |
Wafer Fabrication | Not commercial yet, factories coming |
Packaging & Testing | Several active facilities |
If you’re hunting for real India-made chips, focus on products from government-backed projects or very niche manufacturing. Otherwise, most of what’s called “Made in India” is about value added at the packaging and testing end—still important, but not the whole journey yet.
Challenges Holding India Back
So why hasn’t India jumped straight into the big leagues of semiconductor production yet? If you peek under the hood, the reasons are actually pretty practical and not just some lazy government stereotype. Building a modern chip fab isn’t like opening another smartphone assembly plant—it’s a wildly expensive, insanely complex task.
The cost of one advanced fab can cross $10 billion. That’s just for starters. You also need a chain of reliable partners for supplies like high-purity chemicals, ultrapure water, and 24/7 power—all things India is still ramping up. Then there’s talent. The country definitely has great engineers, but specific semiconductor experience is still rare because nobody’s been doing this at scale here yet.
If you think about gear, the machines that actually etch circuits on silicon are mostly controlled by a tiny global group—companies like ASML in the Netherlands. Getting access, especially to the latest stuff, isn’t easy if you don’t already have deep roots in the business.
Regulations and red tape haven’t helped. Government incentives (like the $10 billion India Semiconductor Mission) have arrived, but many of the big global players are watching to see if things roll out smoothly before they go all in.
Here’s a basic list of the toughest speed bumps right now:
- Upfront Costs: Setting up a chip fab needs billions in investment, long before you even make your first chip.
- Skilled Workforce: India has tech talent but lacks mass experience in high-end chip manufacturing.
- Supply Chain: Most raw materials and specialized equipment still need to be imported.
- Infrastructure: Stable electricity, clean water, and logistics haven’t always matched fab needs.
- Global Competition: Taiwan, Korea, and the US have decades-long head starts and deep pocketed players like TSMC, Samsung, and Intel.
If you’re curious how India stacks up compared to other major electronics manufacturing hubs, check this out:
Country | Number of Leading Edge Fabs (2024) | Share of Global Chip Output |
---|---|---|
Taiwan | 15 | 60% |
South Korea | 8 | 18% |
USA | 12 | 10% |
India | 0 | < 1% |
That gap looks huge, but it’s also the reason there’s so much buzz—and so many eyes—on all these new India semiconductor projects. The nation wants a piece of this action, but it’s going to take serious time and steady progress to actually put a dent in those numbers.
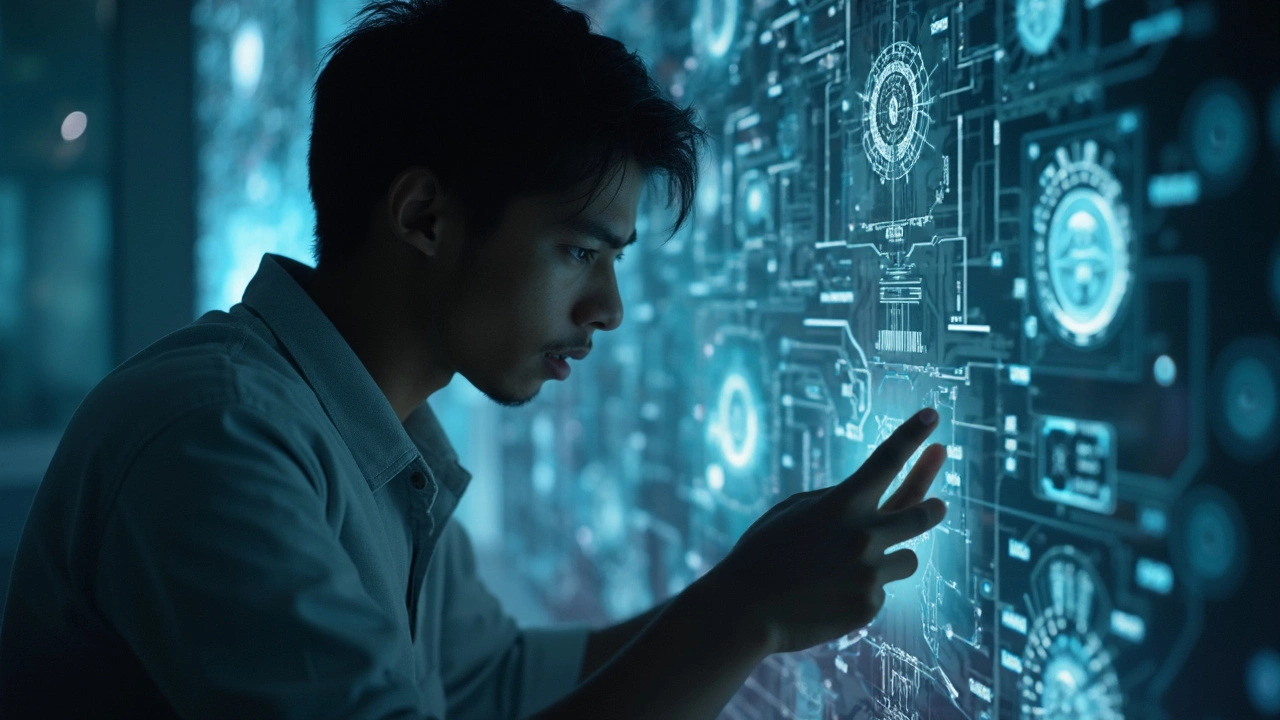
What to Watch If You Care About Semiconductors
If you’re rooting for more India-made semiconductors, or you just want to keep tabs on how the electronics manufacturing India scene is changing, there are a few real-world signs worth keeping an eye on. This isn’t just about government press releases—there are practical things happening right now that actually matter.
- Tata’s Fab Projects: Tata Group’s partnership with PSMC for the Dholera plant is a big one. If that gets built as promised, India could see actual chip manufacturing by 2026. Watch for building updates and any news about equipment getting installed—those are key signs it’s serious and not just talk.
- Micron's Memory Plant in Gujarat: Micron’s assembly and testing facility in Sanand is already up and running. While they aren’t fabricating chips from scratch, their presence puts India on the global chip map for backend work.
- Government Incentives and Policy Updates: The government rolled out a $10 billion semiconductor incentive plan. Check for updates about who’s actually getting the money and breaking ground. Hearing about a “proposal”? Cool, but the real action is when shovels hit dirt.
- Startups and Chip Design: There’s a surge of Indian startups (like Saankhya Labs) designing their own chips here. They usually send these out for production in Taiwan or the US, but it’s still a big step towards local innovation and less dependence on imports.
- Hiring Trends: If you see big companies recruiting engineers for foundry operations or fab construction, it’s a strong hint things are moving forward.
If you like data, here’s a quick look at who’s doing what right now in India’s semiconductor space:
Project/Company | Type | Status (May 2025) |
---|---|---|
Tata-PSMC Dholera | Manufacturing Fab | Construction started, completion by late 2026 |
Micron Sanand | Assembly & Testing | Operational |
ISRO SCL Mohali | Govt. Fab (Legacy) | Operational, Small Scale |
Saankhya Labs | Chip Design | Active, designs manufactured abroad |
Want a tip? Ignore vague headlines about plans and focus on real progress: groundbreakings, equipment arrivals, or engineering jobs—these are concrete signals that semiconductor manufacturing in India is picking up speed, not just making noise.