Manufacturing System Components: The 3 Essentials Everyone Should Know
Think of a factory like a big, complicated recipe. You can't bake a cake without ingredients, the right tools, and a way to get that cake to hungry people. Manufacturing isn't much different, just on a way bigger scale. There are three main parts every system needs to get stuff made and out the door: inputs, the transformation process, and outputs.
You might be surprised at how much government support focuses on these three bits. Ever wonder why certain manufacturing schemes or incentives exist? It's usually to boost one of these core areas—maybe getting cheaper raw materials, improving the machines and methods inside the plant, or making it easier to ship stuff out.
Knowing how these pieces fit gives businesses a real edge. If you understand where things can get stuck—or where cash from the government can help—you can plan smarter and avoid wasting time or money. Let's break each part down and see what really makes a manufacturing system tick.
- Breaking Down the Manufacturing System
- Component 1: Input Resources
- Component 2: Transformation Process
- Component 3: Output and Delivery
- Government Support & Real-World Tips
Breaking Down the Manufacturing System
Ever looked at a smartphone and wondered how it managed to go from random bits of metal and glass to that sleek thing in your pocket? That’s the manufacturing system hard at work. It’s not magic—it’s just a set of steps that every factory relies on, across industries.
Manufacturing systems are designed to take in raw stuff (like metal, plastic, or chemicals), use labor and machines to shape it, and churn out a finished product, whether that's cars, toys, or even chips for your computer. No matter how high-tech or old-school the facility is, every system runs on the same three major components: input resources, the transformation process, and output/delivery.
Here’s how this usually plays out:
- Input resources: These are the materials, labor, machines, and even information needed at the start. Picture this as everything you need before baking a pizza—dough, cheese, oven, even the recipe.
- Transformation process: This is where the work happens. Machines whir, people assemble, and raw materials go through all kinds of changes to become something useful.
- Output and delivery: At the end, you've got the final product. But making sure it gets to the right customer, packaged and on time, is just as important as making it in the first place.
Globally, manufacturing system efficiency is a huge deal. According to a 2024 UNIDO report, countries with well-structured production systems see up to 25% higher output compared to those still stuck on outdated methods. That’s why government schemes often pump money into updating equipment, training workers, or building smarter supply networks.
If you run a business or work in manufacturing, getting a grip on these components helps you spot weak links—maybe you’re spending too much on materials, or bottlenecks in delivery are holding you back. Fixing the right part of your manufacturing system can turn losses into real gains.
Component 1: Input Resources
If you want a steady manufacturing system, you have to start with the right stuff. Inputs are basically everything you need before you can even think about making a product. We're talking raw materials, energy, labor, data, and even good old machines. Miss out on any one of these and things fall apart quickly.
Raw materials are the most obvious. If you're in auto manufacturing, you need steel, plastics, electronics—the works. For food processing, it's all about farm produce and ingredients. But it's more than just stuff you can touch. Energy is a huge input, especially for factories running 24/7. In India, about 30% of a typical manufacturing plant’s cost comes from energy bills. Cut power, and production stops dead.
People are just as important. Skilled workers run the machines, keep quality in check, and solve problems when things go wrong. Even in highly automated industries, you still need technicians to set things up and step in if robots drop the ball. Data and information matter too: design specs, supplier info, even government regulations all feed into the machine.
Here's a quick rundown of the most common input resources for a production process:
- Raw materials and components
- Energy (electricity, fuel, water)
- Labor (from line workers to supervisors)
- Machines and equipment
- Information (software, designs, process data)
Governments know this first step is make-or-break. That's why you'll see all those government schemes targeting raw material access or skill development. For example, India's Production Linked Incentive (PLI) scheme literally rewards companies that use domestic inputs instead of imports. Talk about putting your money where your mouth is.
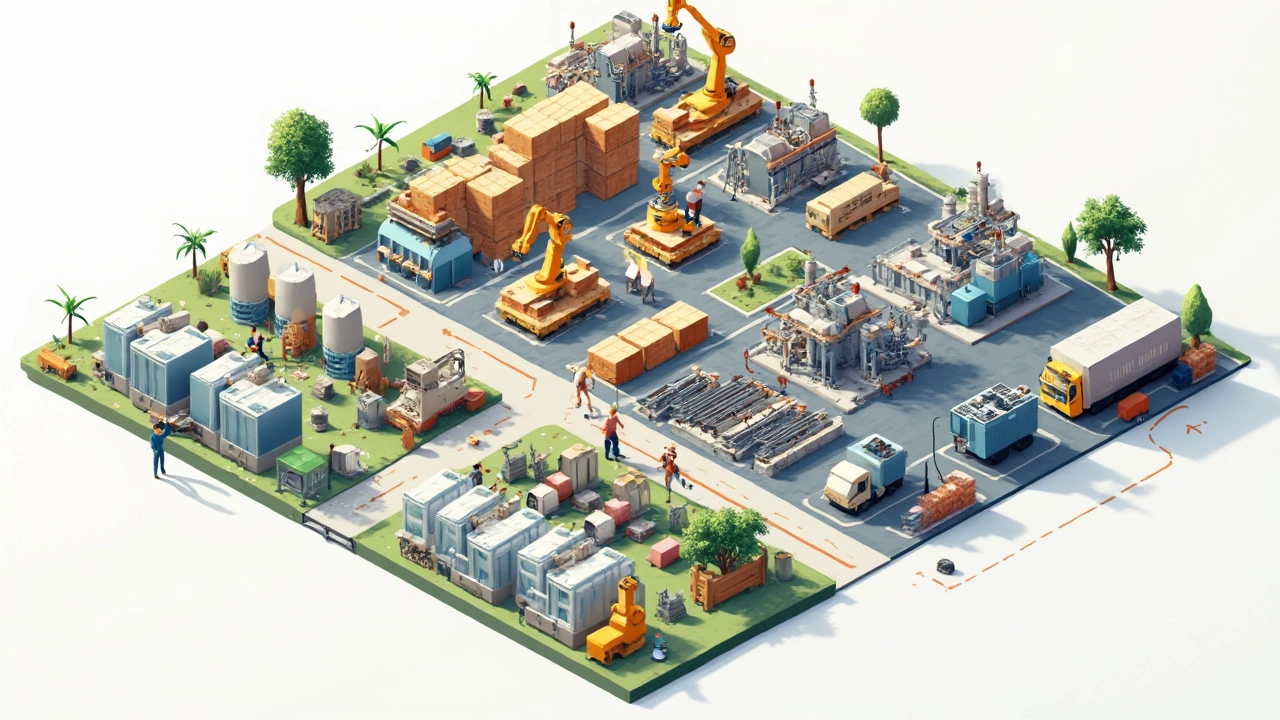
Component 2: Transformation Process
This is where the magic happens in any manufacturing system. The transformation process is all about turning raw materials into final products, using a mix of machines, people, and technology. It's not just about physical work—think of things like cutting, welding, or polishing—but also chemical changes, like baking bricks or mixing chemicals for paint.
Every factory chooses its transformation setup based on what they make. If you’re making cars, you’ll see big assembly lines with robots welding and painting. For food products, you’ll see conveyor belts, slicers, ovens, and lots of checks along the way. No matter the industry, this stage eats up most of the energy and resources. In fact, studies say that about 60% of total manufacturing costs come from this transformation step.
Modern government schemes in manufacturing often push for smarter and greener transformation processes. India’s Production Linked Incentive (PLI) scheme, for example, gives manufacturers bonus payouts when they upgrade to energy-efficient machinery or digitize operations with smart tech.
- Automation: Robots and computer-controlled machines boost speed, cut down errors, and save on labor costs.
- Quality Control: Sensors, cameras, and quick checks catch problems fast, leading to fewer returns and happier customers.
- Lean Manufacturing: Streamlining to cut waste means more profit and better use of inputs.
- Flexibility: Newer manufacturing systems can switch between products quickly, letting factories jump on new trends or meet custom orders.
Here’s a quick look at why upgrading the transformation process pays off:
Change Made | Common Result |
---|---|
Added automation | 15-30% faster output |
Better quality checks | 50% fewer defects |
Lean methods | 10-20% cost savings |
Tuning up your transformation process isn't just for big companies, either. Even small manufacturers can tap into local government programs to get grants or training. It’s all about making the middle of the manufacturing system as smooth and cost-effective as possible.
Component 3: Output and Delivery
The last big piece in the manufacturing system puzzle is getting your finished products out of the factory and into the hands of customers. No matter how smooth your production runs, it means nothing if you can’t deliver quality output on time. This stage turns raw effort into profit—or a headache if you get it wrong.
Output is all about the finished goods, inspection, packaging, and making sure everything matches customer specs. It’s not just what you make, it’s how you handle it before it leaves the building. Skipping on checks or cutting corners here can kill a brand’s reputation fast. A 2023 survey by India’s MSME Ministry found that 78% of small manufacturers who tightened their quality checks reported fewer customer complaints and a 15% bump in repeat orders. That’s direct proof—attention to output pays off.
Delivery is the second half. Now you’ve got to think about logistics, inventory, and transport. Big manufacturers use tech like GPS and real-time tracking to shave hours off shipments. Smaller players often work with logistics partners to keep costs down. Here’s how brands often handle output and delivery:
- Batch Inspection – Sampling finished products before they’re boxed up makes sure nothing sneaks through with a flaw.
- Barcoding and Tracking – Each item gets a unique code so you know exactly where stuff is in the warehouse or on the road.
- Flexible Packaging – Adapting package sizes and materials means you can meet different retailer or export rules without extra hassle.
- Smart Shipping Choices – Pick between rail, road, air, or even drones (yes, really—some government-backed pilot projects now test drone delivery for small high-value goods).
Step | Key Focus |
---|---|
Quality Check | Reduce returns and why customers come back |
Packing | Protecting goods, branding, meeting export rules |
Shipping | Fast routes, cost control, tracking in real-time |
Don’t forget that government schemes sometimes offer support like subsidized shipping for exports, or funding to upgrade warehouse tech. If you’re a manufacturer, staying sharp on output and delivery details doesn’t just save money—it opens new markets and wins loyal customers. Messing up here means more than just late deliveries; it can undo the whole point of great manufacturing.
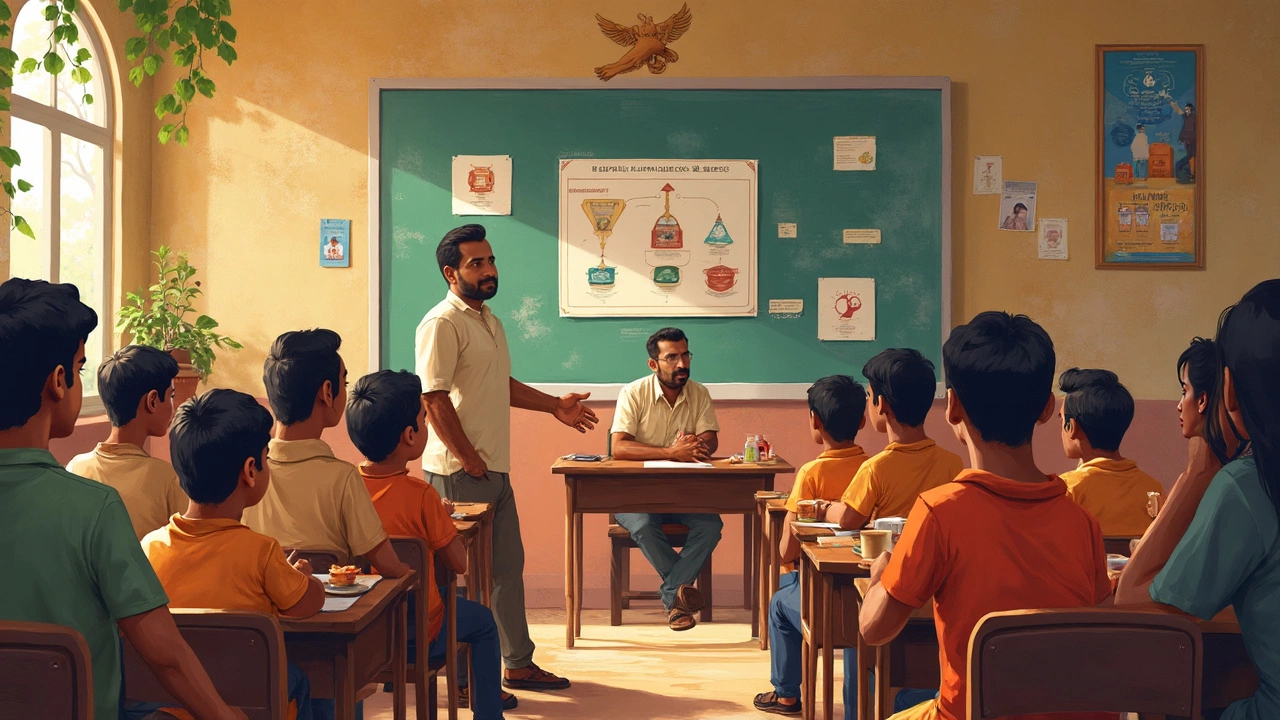
Government Support & Real-World Tips
When it comes to the manufacturing system, government schemes aren’t just window dressing—they pump real resources into the three main components. Let’s look at where the help usually lands and how you can make the most of it.
For input resources, many governments, including India under their Make in India plan, cut taxes on imported machinery and raw materials for certain industries. This can drop total input costs dramatically. India’s Production Linked Incentive (PLI) scheme is a good example, giving direct cash to manufacturers who use local resources and hit certain output targets.
When it comes to the transformation process, a lot of grants and support target tech upgrades. The US, for example, has offered tax credits for robotics and digital manufacturing under the Advanced Manufacturing Partnership program. Using better or automated equipment isn’t just good for numbers. It actually slashes error rates, boosts productivity, and lets you produce more with less hassle.
On the output side, governments often set up export hubs, cut red tape at customs, or offer shipping rebates. Take Vietnam—special economic zones there let manufacturers export goods faster and cheaper because paperwork is sorted in one spot. That keeps stuff moving out instead of collecting dust in a storage bay.
Country | Main Scheme | Focus Component | Unique Benefit |
---|---|---|---|
India | PLI, Make in India | Inputs, Output | Cash incentives, local sourcing boost |
Vietnam | SEZs, Export Rebates | Output | Single-window export process |
USA | AMP, Tax Credits | Transformation Process | Robotics & automation funding |
Now, some real-world tips for manufacturers thinking about government support:
- Read the fine print on any government scheme. Some have requirements like minimum production levels or use of local goods.
- Keep close track of upgrades—tech funding often requires you to prove what equipment changed and the difference it made.
- If you’re in export, look for zones with reduced customs hassle or higher rebates. It can seriously speed up your supply chain.
- Don’t leave free money on the table. Even small cash grants help with margins, especially in tough times.
The most successful manufacturing businesses rarely rely on just one scheme. Mix and match incentives to hit every part of your manufacturing system, and watch those small advantages stack up fast.