Is India Manufacturing Semiconductors? Latest 2025 Facts & Progress
You wouldn’t cross a street on your phone or send a text without relying on something tiny, fragile, and absolutely essential—a semiconductor. The world runs on these chips. Cars, fridges, defence equipment, satellites, your smartwatch, even that clever electric toothbrush. It’s no secret that most have come from places like Taiwan, South Korea, or the US for years. But lately, India’s name keeps popping up in conversations about the global chip rush. Does the future of technology include made-in-India semiconductors, or is all the hype just wishful thinking?
India’s Semiconductor Ambition: Where We Stand Now
The dream of homegrown Indian semiconductors isn’t new. For decades, politicians and tech folks have wanted Indian-made chips powering everything from trains to telecom towers. Until recently, it sounded as remote as blue cows in the Lake District. But in 2021, when the chip crisis went global and car factories shut down for want of a single chip, Indian companies and government offices began to pay real attention. India announced the Semiconductor Mission—a £7.5 billion push to bring chip design, fabrication, and testing to local soil.
The biggest question: are there actual factories making semiconductors in India right now? Honest answer? Not in the way Taiwan’s TSMC or South Korea’s Samsung churn out billions of chips a month. India doesn’t have a full-scale, state-of-the-art semiconductor fabrication plant (fab) spitting out advanced microchips for smartphones or high-end computers—at least not yet. There’s not a single operational commercial foundry today making the sort of chips that run inside your mobile or Xbox. If you pop open your latest Samsung or Apple device, the chip inside wasn’t made in Bangalore, Pune, or Chennai.
But, and this is crucial, the ground is changing fast. In 2023 and 2024, massive investments were announced. Tata Group—think Tatas of Jaguar Land Rover and Tetley Tea—inked partnerships for new fabs, with the most talked-about being in Gujarat. Another big name, Micron Technology (an American memory chip giant), started building a multi-billion-pound chip packaging and testing facility in Gujarat too. But these units, slated to go live between late 2024 and 2026, will mostly handle assembly, testing, marking, and packaging (ATMP)—not core chip-fabrication at microscopic nanometer levels. Still, it’s a big start.
Here’s a quirky bit: India has made some semiconductors for specialised use before. Take SCL (Semi-Conductor Laboratory) in Mohali. This government-run factory made chips for ISRO (India’s NASA) and certain defence projects. Think old-school chips, not the snazzy stuff in your iPhone 16. These are mainly for satellites, weather stations, scientific research—places where longevity beats bleeding-edge speed. SCL got a government rescue in 2022, with a £500 million tech upgrade planned, so it might edge towards more modern chip production soon.
To sum up, while there are no world-class advanced fabs operational in India yet, there are major facilities under construction, serious corporate money on the table, and plenty of official determination. Real "Made in India" chips, with significant volumes, are just a few years off.
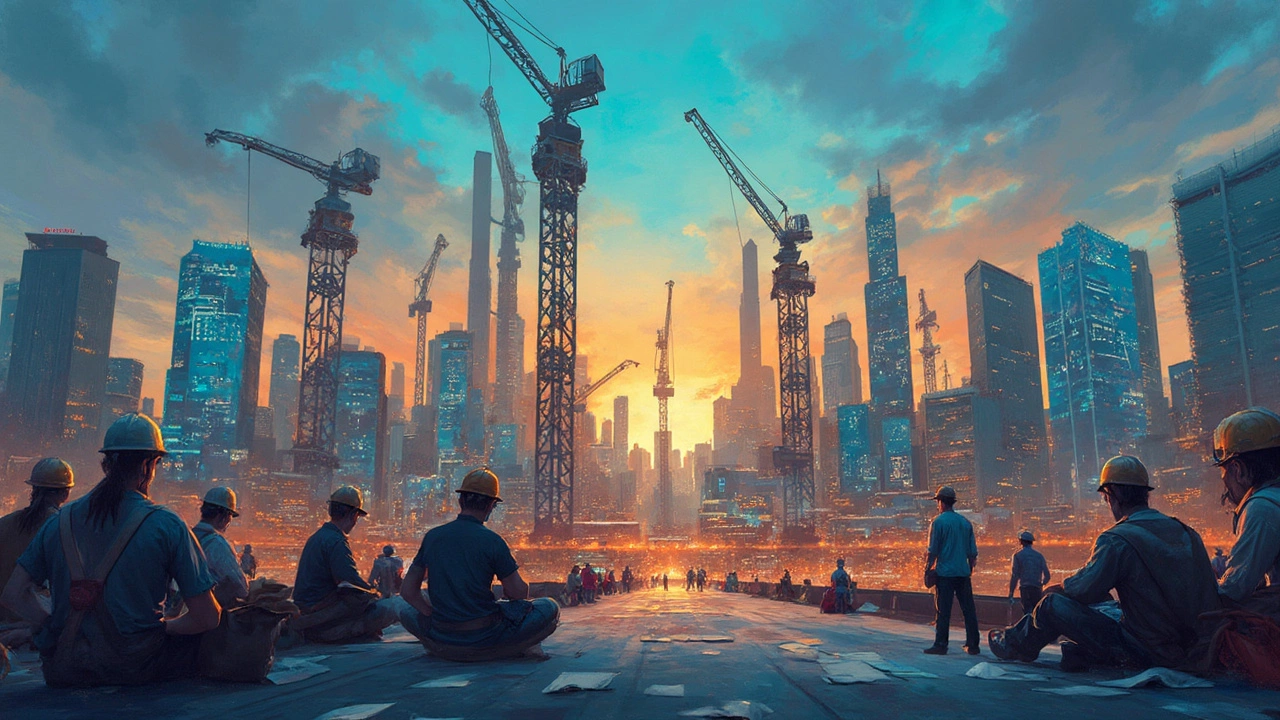
Why Is Making Semiconductors in India So Tricky?
Building a chip factory is like assembling a Mars mission on Earth. It costs billions to set up, and one minor speck of dust can ruin a whole batch of chips. India has fierce engineers—it churns out more STEM graduates than nearly anywhere else—but chipmaking needs an entire chain: engineers, skilled machine operators, water, clean electricity, chemicals, rare gases, and a supply chain tighter than your nan’s spending money at Tesco.
India’s biggest roadblock has been its lack of fabrication knowhow. Places like Taiwan spent four decades perfecting the art, protecting trade secrets, and pulling every lever to nurture chip specialists. India, in contrast, grew up as the world’s top spot for software, IT, and chip design—not manufacturing. You’ll find thousands of sharp designers in Gurgaon or Hyderabad working on blueprints for chips used by Qualcomm, MediaTek, or Intel, but the real silicon slicing always happened elsewhere.
Then you have the daunting cost. A brand-new fab for leading-edge chips (the ones in your phone, at sub-10nm scale) costs around £10-15 billion and often demands government hand-holding. India’s new incentives help. Government-backed land offers, tax breaks, customs holidays, and ready-to-go utilities in special technology zones like Dholera or Sanand have pulled in foreign partners. But getting a factory off blueprints and into steady volume production is still tough. India also faces water woes—fabs gulp up millions of litres per day, and some regions don’t have that to spare.
No less tricky: the input materials. Chipmaking isn’t just about sand and smarts—India has to import nearly all specialty chemicals and precision equipment, thanks to export controls from the US or Japan. Getting permission to import a single photolithography machine can take months. Vendors like ASML (from the Netherlands) guard their technology like dragons sitting on gold.
Cultural and regulatory speed bumps matter too. Setting up a semiconductor factory in India means cutting through complicated land acquisition, environmental approvals, and local politics. Micron’s Gujarat project, for example, got the green light thanks to national and state government working overtime to clear red tape. Not every future project will get such a royal welcome.
Yet, despite all these obstacles, the signs point to a slow but steady climb. Indian universities are launching chip-focused engineering tracks. Companies like Tata and Vedanta are headhunting chip experts from abroad, dangling rich paychecks and relocation benefits. In a twist, even local startups in Pune and Noida have started working on chip design and embedded systems, hopeful that a homegrown fab will soon let them take ideas from paper to product.
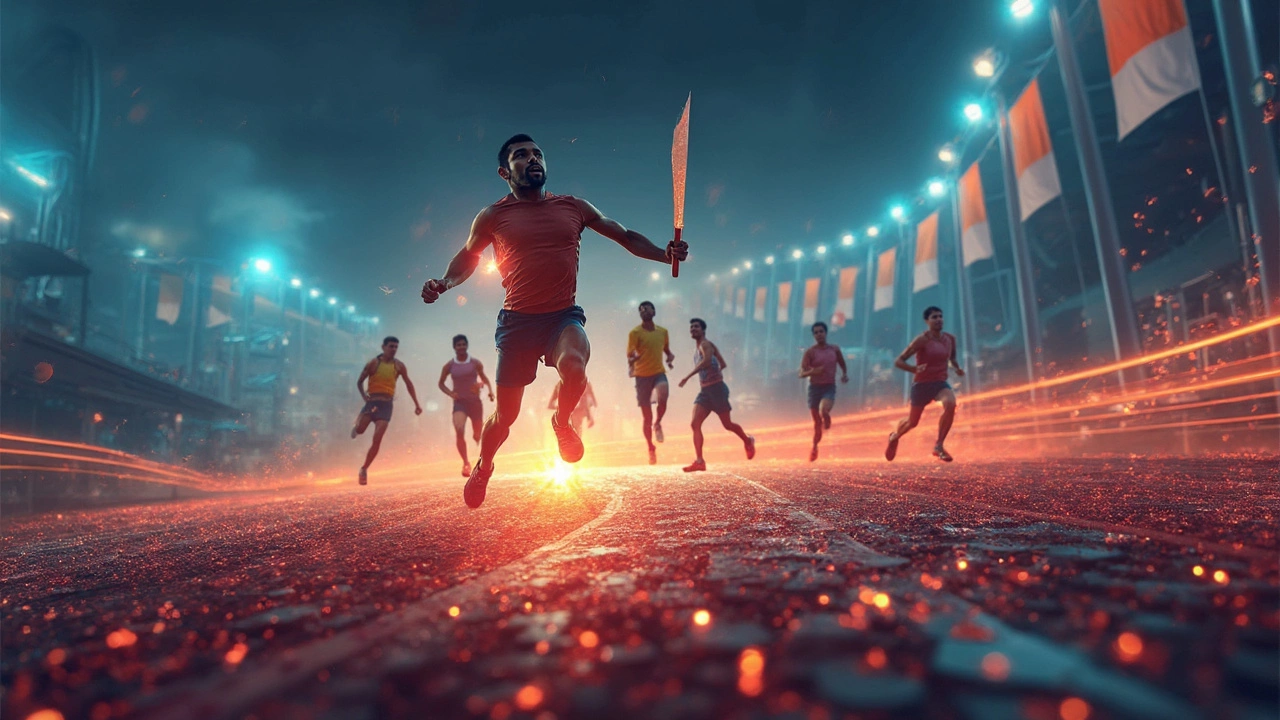
What Will Indian-Made Semiconductors Change for the World?
Big question: if India takes its shot and starts mass-producing semiconductors, does that actually shake up the global chip table? Absolutely, especially with Asia increasingly being the world’s hardware backyard. First off, it would lower India’s gigantic electronics import bill—chips are the second biggest import after oil. Making more chips locally reduces exposure to supply chain shocks (like COVID lockdowns or Taiwan-China tensions). You’d see cheaper gadgets and cars in Indian markets, but also a nudge towards exporting Indian brand chips, especially to countries trying to escape single-vendor reliance.
You’ll hear folks at industry events in Bengaluru or London saying an Indian foundry can't outgun TSMC or Samsung overnight. Right now, even if Tata’s Gujarat fab goes live in late 2025 as scheduled, it’ll likely churn out older-generation chips first—say, for household appliances, basic cars, or industrial gear. Racing into advanced 3nm or 5nm chips for high-specced smartphones or AI servers will take longer. Still, even starting with so-called legacy nodes matters: a shortage of these types hampered the global auto sector during the last crisis.
It’s a smart play for India’s growing electric vehicle market too. Cars need lots of dependable, rugged chips. India already assembles millions of cars and e-scooters every year. Local chipmaking means fewer production pauses for want of a chip—or less dependence on China for critical parts. For defense tech, having a trusted, domestic chip supply is nothing short of vital.
If you’re thinking globally, the real kicker is new jobs and a whole bouquet of new expertise. Setting up one fab creates thousands of direct and indirect jobs, from chemical engineers and maintenance techies to local suppliers and logistics crews. India’s own engineers, who had to fly to Singapore, Germany, or Taiwan for chip jobs, could soon build careers closer to home.
There’s even talk that India might focus on certain specialised chips—such as power management ICs, automotive microcontrollers, or sensors for IoT. Instead of trying to beat Samsung at the smartphone chip race, India could quietly become a world leader in chips that power green energy and smart cities.
It’s not all smooth sailing ahead. Chipmaking is a marathon, not a sprint. You need reliable electricity, pure water, stable policy, and a talent pool that grows richer every year. But the country has shown surprising grit in other tech sectors before—just look at how Indian telecom leapfrogged into 5G or how local players built a payments network that makes UK’s seem positively Victorian.
So, are semiconductors made in India right now? Not the ones in your pocket or on your desk—yet. But the odds are changing fast. Give it another year or two, and you’ll likely see the words “Made in India” etched into chips powering everything from your hairdryer to your neighbour’s new SUV.